Introduction
Interlining provides a shape and structure to your garments. Therefore, it is important to maintain the quality of your interlining. Some interlinings can face quality problems. If these problems aren’t resolved, they can impact the purpose of interlining. For example, you might not be able to achieve the shape or structure that you desire.
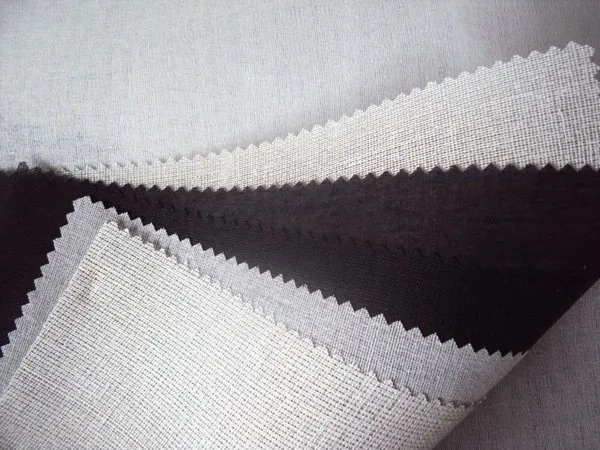
There can be multiple problems that occur in your interlining and outer fabric. Some of these problems can occur due to the following reasons:
- The fusible interlinings cloth got low quality.
- The adhesives used for interlining didn’t perform well.
- The fusing or stitching of interlining material is not done correctly.
- Or, you just selected the interlining that weighs more than your cloth or doesn’t match the base fabric.
You should know that if base fabric properties don’t match the interlining cloth, it will not yield the desired results. So when you choose an interlining, keep in mind all these factors.
All these problems are possible when using the interlining for your garments. However, the most common problem that occurs in interlining is due to adhesives. For example, you can see bubbling in the adhesives in interlining. Apart from bubbling problems, rippling can also occur in fusible interfacing. So how do you solve all these problems?
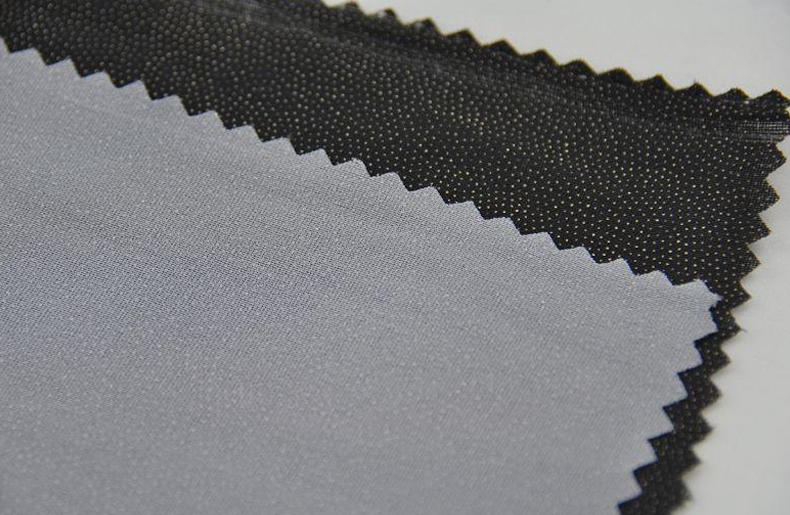
Look no further if you have the same problem in your fusible interlining. This article will help you learn everything about it.
What Is Meant By Bubbling In Interlining?
Careful inspection of your garments can reveal the bubbling in your interlining. Bubbling is also known as delamination. Simply put, you can say that lack of a strong bond between the shell fabrics and interlining is called bubbling. Or, when the bond between the shell fabric and interlining breaks down, it refers to bubbling or delamination.
Interlinings are normally found in areas that require more support and stiffness. For example, you can find them in front of jackets, collars, or cuffs. You grabbed one of your favourite shirts and found bubbles on its collars. It is when the woven interlining starts separating from your shell fabric.
When you fuse the woven interlinings on the wrong side of the fabric, there are chances to cause bubbling or rippling in the fusing process. You want to get results for providing stiffness or support to your interlining, but bubbling can ruin it all.
When the resin becomes embedded in the interlining substrate instead of the base fabric, it causes bubbling. It is because the resin migrates to the heat, which prevents a strong bond between the shell fabric and interlining. You can see that the base fabric will appear to be delaminated or bubbled. Do you want to know the causes of bubbling in interlining? Continue reading.
What Are the Causes Of Bubbling In Interlining?
Well, there might be several causes of bubbling or delamination in your interlining. As mentioned, when the resin migrates towards the heat, it weakens bonding. Bubbling often results from incorrect garment manufacture of interlining fabric with your base fabric. The wrong manufacturing in terms of pressure, temperature, and time can result in bubbling.
The best way to detect bubbling on your interfacing is to try ironing it. When you iron your bubbled interfacing, it will not appear smooth. Some common causes of bubbling in interlining are:
Poor bonding of fused fabric assemblies
Differential shrinkage also cause bubbling in interlining
Uneven temperature or pressure during garment construction
Inconsistent use of resins, etc.
Not enough time is given to fuse interfacing with fabric.
The temperature, time and pressure parameters of the gluing machine are not properly adjusted during gluing. The temperature is not enough, the rubber is not fully melted, resulting in low peel strength, will bubble, the temperature is too high, the rubber aging, resulting in low peel strength, will bubble, time is not enough, the rubber is not fully melted and permeated into the fabric fiber, resulting in low peel strength, will bubble, too long, the rubber aging, resulting in low peel strength. The pressure is too low, after the glue melts, it does not penetrate into the fabric fiber, resulting in low peeling strength and foaming. The pressure is too high, and the glue is too much squeezed into the fabric fiber after melting, which will cause too little glue between the fabric and the interlining, resulting in low peeling strength and foaming.
Bubbles in interlining are formed due to the glue used to fuse interlining to your fabric. The glue has shrunk, stretched, or bubbled when you dry clean the fabric.
You should note that bubbling doesn’t reveal in sewn interlinings just after you buy the garments. It reveals after several washes or dry cleaning of your clothes. It can also result from the age of your garments or sewn interlining. Before accusing your laundry man of damaging your clothes, you should understand why it happened in the first place.
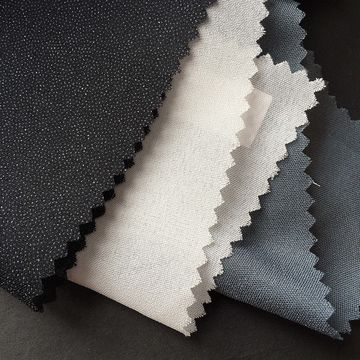
The laundry man has nothing to do with bubbling in the interfacing of your knitted fabrics. It happens due to the wrong manufacturing and usage of interlining in your garments—poor adhesion during the heat press portion of interfacing results in bubbling. Some other reasons that cause bubbles in your interlining are:
✓The iron wasn’t hot enough when you fused garment parts to the base fabric.
✓You didn’t apply enough pressure through iron on the interfacing.
✓The finish on the iron repelled the interlining glue.
✓You used too much steam before applying pressure on your knitted interlining.
✓You moved the fused fabric while it was still hot.
✓You didn’t press out the wrinkles before you applied interlining on the upper fabric.
✓You used too much hot iron that shrank the fabrics.
✓You didn’t give it enough time to fuse with the delicate fabric.
Is There A Way To Avoid Bubbling In Interlining Materials? If Yes, How?
If you just found bubbling in your interlining, you must want to remove it. You should note that ripping it off is the best thing you can do. You can’t just make it fine by pressing the iron. Remove the bubbled interfacing and replace it with a new interlining on the shell fabric.
You can minimise the damage if your interlining shrinks or damages after it is fused or sewn. But you can never completely cure the bubbling in interlining.
You should avoid keeping your garments at temperatures more than 150 degrees F. It is the temperature where your interlining starts separating from the shell fabric.
When buying garments, you should check the interlining areas to see if there is bubbling. Figuring it out at the right moment can save you from wasting money.
When fusing new interfacing in your garments, you should use a different type than the previous one.
One of the biggest reasons to cause bubbles in interlining is the lack of pre-shrinking. When you don’t pre-shrink your base fabric and interfacing, they result in problems like bubbling. Pressing the garment’s layers with heat pulls off the other layers due to bubbling. Therefore, it is highly recommended to pre-shrink your interfacing and the base fabric.
To shrink your fabrics, you need to put them in warm water for a particular duration. You must get out the fabric and interlining when the water is cooled. Then, put them somewhere for drying.
You should first test a scrap of interlining on a scrap of the base fabric. It will ensure that your interlining is perfectly aligned with the base fabric.
Why Should You Avoid Bubbling In Interlining?
Bubbles in your interlining can have a bad impact on your garments. You waste money if you find your newly bought garments with bubbles. Some disadvantages of bubbling in interlining are:
✓Lack of enough support
✓Lack of stiffness in your garments.
✓Wrinkles appear in garments, making them look uglier.
✓Lowers the quality of fabrics
✓It shrinks the fabric making it hard to fit your size.
These disadvantages can tell you why you should avoid bubbling in interlining. So make sure you take all preventive measures to avoid bubbling in interlining. Talk to an expert or your manufacturer for some authentic solutions.
Suppose you are a wholesaler and find your customers complaining. In that case, you need to talk to your manufacturer since it is the manufacturer’s responsibility to take care of these things when applying interfacing to the fabric.
What Other Problems Occur In Interlining?
Interlining can do magic to your garments, but applying it incorrectly can cause several problems. These problems mostly occur during its operation with the base fabric. The most common reasons behind it are time, pressure, and temperature. If you don’t consider them carefully, they can cause problems that are listed below:
✓Strike through
✓Strike back
✓Shrinkage
✓Colour changing
✓Boards
✓The improper fusing of interlining on the base fabric
✓A glue mark is visible on the surface.
✓Pleat on process
All these problems can degrade the quality of your garments, affecting your company’s reputation. Ensure you take the necessary measures when applying the interlining on your garments. You must also choose the right type of interlining for your garments. In most cases, the problems occur when you don’t select the right type of interlining.
You should know which interlining can best match your base fabric. To know this, you must focus on factors such as quality, weight, fabric, etc. You also need to consider which garment you will use with your interlining.
Conclusion
Bubbling in interlining can make your garments look uglier. Therefore, you should make sure to avoid these problems in your interlining. Contact Us now if you are a wholesaler looking to buy interlining from a high-quality manufacturer. We take special care of quality controls to manufacture high-quality interlining.
You can also tell us your requirements so we can manufacture interfacing according to your garments.